【description】:the winding mandrel shall be selected according to the outer diameter of the product, as shown in the table below. for the data in the table, the winding pins of different mandrel shall be selected. after winding, the element can be put into
aluminum electrolytic
capacitor element winding is also called wrapping and element winding.
it is to wrap the cathode aluminum foil and anode aluminum foil with electrolytic paper, and then use paste (made of polyvinyl alcohol) or adhesive tape to make aluminum electrolytic capacitor
1. winding process and technical requirements:
1.1, anode foil and cathode foil overlap is good, if the anode foil and cathode foil overlap is not good, will cause the following phenomenon
a, the "effective" area (overlapping part) of the metal plate of the capacitor decreases, resulting in the decrease of the capacitance.
b, after winding, the element core pulling, as shown in the following figure
c, the prime is spiral, as shown below
1.2. the center point of the well wound prime and the two leads shall be in line without eccentricity, as shown in the figure
bad winding condition, 4 legend
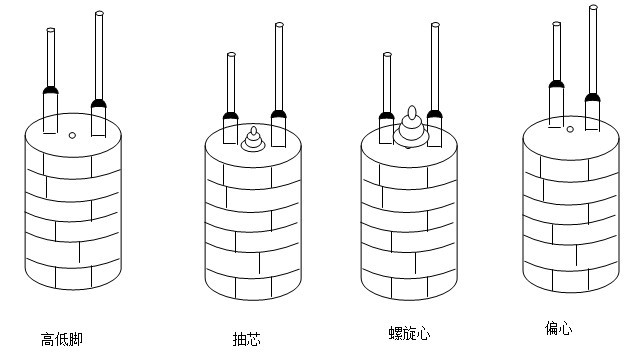
1.3. the distance between the two leads of the prime element and the distance between the holes of the sealing rubber plug shall be matched, otherwise, poor sealing will be caused, and leakage will be caused in serious cases, as well as the scratch (open circuit, semi open circuit) on the contact between the aluminum tongue and the aluminum foil, which will greatly shorten the service life of the capacitor.
the winding mandrel shall be selected according to the outer diameter of the product, as shown in the table below. for the data in the table, the winding pins of different mandrel shall be selected. after winding, the element can be put into the aluminum shell smoothly, and a certain gap shall be reserved with the aluminum shell
shell diameter / mm, ultra small, 5, 6, 8, 10, 13, 16, 18, 22
mandrel diameter / mm 0.8 ~ 1.01.2 ~ 1.51.5 ~ 1.8 1.82.0 ~ 2.53 3.5 ~ 4 3.5 ~ 4 3.5 ~ 4